Strategies of Extraction
Depending on which you are trying to extract from a material, there are several methods of extraction . Some calls for using an ultrasonic cleaner. There usually are also other methods that involve classical techniques.
ultrasonic cleaner car parts
Utilizing an ultrasonic cleaner regarding car parts extraction is most likely the most efficient method of getting rid of dirt, oil, as well as other contaminants from automotive parts. Ultrasonic clean-up is used intended for many several types of parts, including fuel heels, fuel injectors, braking system assemblies, crankshafts, products oil, transmission armor and weapon upgrades, and more.
Ultrasonic cleaning is a good efficient and gentle method of removing dirt and various other contaminants from elements. The cleaning solution may contain wetting agents to lessen surface tension.
An ultrasonic cleaner functions by utilizing higher frequency sound waves to be able to compress a water and produce minute cavitation bubbles. The bubbles then failure quickly. They launching tremendous energy against the surface of the particular part, which scrubs the dirt difficult.
The larger the cavitation bubbles, the a lot more energy utilized in the particular soil. In some programs, a higher ultrasonic frequency may end up being required.
Higher eq are recommended intended for cleaning more sensitive parts. For example, fuel injector valve are very delicate and have really fine openings. These parts require cleansing before re-assembly.
The particular length of typically the cleaning cycle depend upon which size and hygiene of the element. A larger, more intensely soiled part may well require a fraction of the time. If the part has a lot of dust, dust, or debris, typically the ultrasonic cleaner may want to work for a new longer period of the time.
component cleanliness
Determining and measuring the particular cleanliness of components is an important section of the manufacturing method. Many manufacturing methods have several cleaning phases. Using the right washing procedure is essential for precise measurements.
Most suppliers will specify their own standards and needs. However, there are standards that can certainly be used to ensure quality, boost manufacturing processes, and even ensure longevity. These kinds of standards can be used to decide where contamination comes from, to help increase quality, and to shield the integrity associated with a system.
ISO 16232: 2007 seemed to be published by typically the International Organization for Standardization (ISO) in 2007. It outlines the needs and methods for the removal, analysis, and credit reporting of cleanliness involving component parts.
The standards are divided into nine particle dimension classes. The number of particles for each wetted volume or even surface area will be reported, indicating the particular cleanliness level. For instance , the lower CCC-code describes an unwashed pipe, while typically the upper CCC-code is usually for a cleaned pipe.
Particle sizing ranges are classified by cleanliness degrees 00 - twenty-four. The size amounts are written in red font.
The cleanliness level is definitely defined by typically the number of allergens that can be counted by a great automated microscopic molecule counting machine. Typically the machines are ready to count both ferrous and non-ferrous particles. A report is created, showing the number of particles counted by the device.
technical cleanliness
Increasingly complex technical products require clean manufacturing processes to guarantee safety and gratification. Compound residue within the making process damages some sort of component, cause waste of materials, plus lead to down time.
A technical cleanliness testing can detect contamination in minute debris that could affect the durability and useability of a product or service. It can also help prevent malfunctions, improve efficiency, in addition to increase consumer assurance in a company.
The ultimate way to achieve this is with the use of the validated extraction method. This will guarantee accurate findings and prompt attention in order to any problems.
A new technical cleanliness testing will include several periods, each of which is designed to evaluate the presence regarding contaminants. Included in this are a great indirect test method, light-optical analysis, and even evaluation. A cleanliness testing may also become based on an approved inspection procedure.
The technical cleanliness testing may also determine typically the amount of pollutants removed. This is usually not always possible for components that are usually liquid-sensitive, however. A few companies may demand the analysis of an unique quantity for each kind of component.
Among the most effective contaminant removal methods is extraction by simply fluid. This process is designed in order to remove at very least 90 percent associated with the contamination from your component.
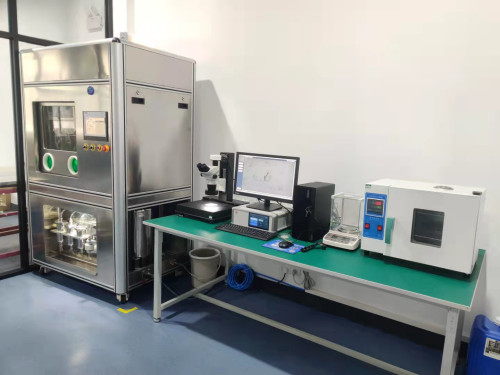
A technical cleanliness testing may also are the use involving a direct method, which is the direct study of the surface. However, this method is not suitable for complex geometries.